Harrison TU150P Fault
Moderators: Martin, Steve, Mr Magoo
Harrison TU150P Fault
Hi Guys.. Can you help?
Our TU150P is having a student created problem.. it has an "410 servo alarm: x exess err" displayed on screen.
From what i understand, after setting z zero to the billet, he was homing the machine but pressed x+ which ploughed the tool into the job!
Tried the IT solution" turn it off and on again" but no change!
Any fixes you can suggest?
Mark
Our TU150P is having a student created problem.. it has an "410 servo alarm: x exess err" displayed on screen.
From what i understand, after setting z zero to the billet, he was homing the machine but pressed x+ which ploughed the tool into the job!
Tried the IT solution" turn it off and on again" but no change!
Any fixes you can suggest?
Mark
- Denford Admin
- Site Admin
- Posts: 3644
- Joined: Fri 10 Feb , 2006 12:40 pm
- Hardware/Software: Go to User Control Panel > Profile
Enter as much information about your CNC hardware and software as you can - it makes it easier for everyone to know what you're talking about then. - Location: Sunny Brighouse
- Contact:
Re: Harrison TU150P Fault
Check the fuses and circuit breakers.
Excess errors usually mean that the motor should be moving but the control dosn't see anything back from the encoder.
Excess errors usually mean that the motor should be moving but the control dosn't see anything back from the encoder.
Re: Harrison TU150P Fault
Thanks for the quick reponse admin..
Have checked all fuses we know of.. shown as F1, F6 - F9! No fault!
Check switched off and reset all breakers!
Rebooted machine and still showing same error message!
Any other advice?
Mark
Have checked all fuses we know of.. shown as F1, F6 - F9! No fault!
Check switched off and reset all breakers!
Rebooted machine and still showing same error message!
Any other advice?
Mark
- Denford Admin
- Site Admin
- Posts: 3644
- Joined: Fri 10 Feb , 2006 12:40 pm
- Hardware/Software: Go to User Control Panel > Profile
Enter as much information about your CNC hardware and software as you can - it makes it easier for everyone to know what you're talking about then. - Location: Sunny Brighouse
- Contact:
Re: Harrison TU150P Fault
After another look at the book, 410 alarm means that the X axis position deviation is too great when at stopped.
The amount of movement (probably in microns) is set in parameter 593 (X) and 594 for the Z axis.
Check this and even set it to say 10,000 to see if it jumps 10mm when you power on (ie, before the 410 alarm kicks in again)
It could still be that the drives aren't energised and the excess movement (when shoud be stopped) is due to the X axis dropping - is there a brake on that axis ? Can you hear it come off just before the error pops up ?
The amount of movement (probably in microns) is set in parameter 593 (X) and 594 for the Z axis.
Check this and even set it to say 10,000 to see if it jumps 10mm when you power on (ie, before the 410 alarm kicks in again)
It could still be that the drives aren't energised and the excess movement (when shoud be stopped) is due to the X axis dropping - is there a brake on that axis ? Can you hear it come off just before the error pops up ?
Re: Harrison TU150P Fault
No brake in the system!
Looked at the parameters, 593 and 594 show as zeros
Have checked out our machine manual and those numbers dont show up!
What actual figures should be inputed into the parametersproduce the 10mm jump?
Thanks
Mark
Looked at the parameters, 593 and 594 show as zeros
Have checked out our machine manual and those numbers dont show up!
What actual figures should be inputed into the parametersproduce the 10mm jump?
Thanks
Mark
- Denford Admin
- Site Admin
- Posts: 3644
- Joined: Fri 10 Feb , 2006 12:40 pm
- Hardware/Software: Go to User Control Panel > Profile
Enter as much information about your CNC hardware and software as you can - it makes it easier for everyone to know what you're talking about then. - Location: Sunny Brighouse
- Contact:
Re: Harrison TU150P Fault
I'm not sure then - that info was for an 0TC control - what's yours ?
Have seen this thread ?
viewtopic.php?f=53&t=982&hilit=410
It sounds like a similar issue, but I'm not sure what that #545 parameter did - it dosn't appear in my book - the listing jumps from #0543 to #0548
Have seen this thread ?
viewtopic.php?f=53&t=982&hilit=410
It sounds like a similar issue, but I'm not sure what that #545 parameter did - it dosn't appear in my book - the listing jumps from #0543 to #0548
Re: Harrison TU150P Fault
Machine info is as follows:
Harrison TU150P
Built 1994
Serial No. TP0015
Software ver. 7.7D
GE Fanuc OT
Manual says that its model A
Harrison TU150P
Built 1994
Serial No. TP0015
Software ver. 7.7D
GE Fanuc OT
Manual says that its model A
- Denford Admin
- Site Admin
- Posts: 3644
- Joined: Fri 10 Feb , 2006 12:40 pm
- Hardware/Software: Go to User Control Panel > Profile
Enter as much information about your CNC hardware and software as you can - it makes it easier for everyone to know what you're talking about then. - Location: Sunny Brighouse
- Contact:
Re: Harrison TU150P Fault
I don't have access to a 0T-A maintenance manual at the moment (as we're moving)
Can you find the alarm in your manual ? It will usually give you some idea what parameters or diagnostics are related to the issue.
Regardless of parameters however, the alarm is saying that the machine is moving when it shouldn't be - can you see / hear what happens when you power up the drives ? What about any alarm LED's on the axis drives ?
The axis would move when it should be stationary because:
a. the drive is faulty and is not responding to the analogue position command
b. the drive or motor is faulty and moves erratically (eg if a thyristor has blown)
c. the analogue command to the drives is faulty or wired the wrong way round
d. the encoder position feedback signal is faulty (unlikely though as the control must be seeing movement to cause the alarm)
Can you find the alarm in your manual ? It will usually give you some idea what parameters or diagnostics are related to the issue.
Regardless of parameters however, the alarm is saying that the machine is moving when it shouldn't be - can you see / hear what happens when you power up the drives ? What about any alarm LED's on the axis drives ?
The axis would move when it should be stationary because:
a. the drive is faulty and is not responding to the analogue position command
b. the drive or motor is faulty and moves erratically (eg if a thyristor has blown)
c. the analogue command to the drives is faulty or wired the wrong way round
d. the encoder position feedback signal is faulty (unlikely though as the control must be seeing movement to cause the alarm)
Re: Harrison TU150P Fault
Have 2 of these TU's here so have run them at same time to compare!
No differances between them during boot up, but when checking the LED's in the back we have!
Our faulted machine has XDFR and ZDFR LED's illuminated, but our working machine also has XER and ZER!
Does that point me in any direction?
Mark
No differances between them during boot up, but when checking the LED's in the back we have!
Our faulted machine has XDFR and ZDFR LED's illuminated, but our working machine also has XER and ZER!
Does that point me in any direction?
Mark
Re: Harrison TU150P Fault
Looking at manual again..
Alarm 410
Servo alarm
Contents: In x-axis, the position deviation amount during stop is greater than the setting value.
Remarks: T or M.
It also provides a Note: It is necessary to set the limit value to newly added parameter no 593 - 596.
Alarm 410
Servo alarm
Contents: In x-axis, the position deviation amount during stop is greater than the setting value.
Remarks: T or M.
It also provides a Note: It is necessary to set the limit value to newly added parameter no 593 - 596.
- Denford Admin
- Site Admin
- Posts: 3644
- Joined: Fri 10 Feb , 2006 12:40 pm
- Hardware/Software: Go to User Control Panel > Profile
Enter as much information about your CNC hardware and software as you can - it makes it easier for everyone to know what you're talking about then. - Location: Sunny Brighouse
- Contact:
Re: Harrison TU150P Fault
I'm guessing that XER is X Enable Relay (which obviously won't come on until the fault is cleared.)
The drive(s) must not be powering up or have fault lights on them ?
Are you sure you've checked every fuse and Circuit breaker you can find ?
Sorry if you already know this but sometimes fuses are behind black caps, screwed into the terminal rail
The drive(s) must not be powering up or have fault lights on them ?
Are you sure you've checked every fuse and Circuit breaker you can find ?
Sorry if you already know this but sometimes fuses are behind black caps, screwed into the terminal rail
Re: Harrison TU150P Fault
I would check parameters 544 & 545 & set them both to 0.
If the Fanuc control detects a collision it alters these parameteres.
544 = X axis
545 = Z axis
If it is down to this then on power up you will see that one or both of the axis jump a couple of mm. This then trows up the detection error which dissables the XER & ZER relays.
If the Fanuc control detects a collision it alters these parameteres.
544 = X axis
545 = Z axis
If it is down to this then on power up you will see that one or both of the axis jump a couple of mm. This then trows up the detection error which dissables the XER & ZER relays.
Re: Harrison TU150P Fault
Have checked
F1 - F2 on INPUT UNIT
F1, F6 - F9 between TRUNKING E and D
F12 - F13 on POWER UNIT
During bootup:
The SO and SI LED's illumiate on the OT-A Control board
The XER and ZER LED's flash on, then off again!
The SI LED switches off leaving just the SO LED on.
Have located the drive boards (pic) and only 1 amber LED is shown operating on each board!
Have check the 3 fuses built into each drive board.. all ok!

F1 - F2 on INPUT UNIT
F1, F6 - F9 between TRUNKING E and D
F12 - F13 on POWER UNIT
During bootup:
The SO and SI LED's illumiate on the OT-A Control board
The XER and ZER LED's flash on, then off again!
The SI LED switches off leaving just the SO LED on.
Have located the drive boards (pic) and only 1 amber LED is shown operating on each board!
Have check the 3 fuses built into each drive board.. all ok!

- Attachments
-
- 2010-12-14 16.22.20.jpg (2.54 MiB) Viewed 13716 times
Re: Harrison TU150P Fault
have check parameters 544 and 545 and both are at showing all zeros
Re: Harrison TU150P Fault
Does the X axis move on power up? (1 to 2 mm)
It may be 544 is the wrong parameter.
It may be 544 is the wrong parameter.
Re: Harrison TU150P Fault
Have just powered up to check x axis movement during power on!
Each time it powers up it does seem to move or even twitch -0.1 or similar.. press alarm reset and i repeats!
Each time it powers up it does seem to move or even twitch -0.1 or similar.. press alarm reset and i repeats!
Re: Harrison TU150P Fault
It does sound like it's the collision parameter.
Can you compare other parameters?
554,555
Can you compare other parameters?
554,555
Re: Harrison TU150P Fault
After some long reading of the machine manual, the advice from this forum and giving myself a mental beating, we have found the error!
The 544 and 545 parameters have now been reset to zero and the machine is working! Been looking at the diagnosic pages!
Thanks for all your help!
Mark
The 544 and 545 parameters have now been reset to zero and the machine is working! Been looking at the diagnosic pages!
Thanks for all your help!
Mark
- Denford Admin
- Site Admin
- Posts: 3644
- Joined: Fri 10 Feb , 2006 12:40 pm
- Hardware/Software: Go to User Control Panel > Profile
Enter as much information about your CNC hardware and software as you can - it makes it easier for everyone to know what you're talking about then. - Location: Sunny Brighouse
- Contact:
Re: Harrison TU150P Fault
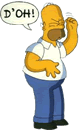
Glad it's sorted now